As brands and retailers experience growing demand for the latest consumer products, the resulting increase in production and batch sizes makes quality control more challenging for companies.

Traditional compliance testing techniques can sometimes provide limited pass/fail information, which results in insufficient measurements on the batch’s quality control, identification of the root cause of failure results and overall quality assurance (QA) in the production process.
Intertek combines legal, customer and essential safety requirements to customize a workable QA process, called Statistical Quality Assurance (SQA). SQA is used to identify the potential variations in the manufacturing process and predict potential defects on a parts-per-million (PPM) basis. It provides a statistical description of the final product and addresses quality and safety issues that arise during manufacturing.
SQA consists of three major methodologies:
- Force Diagram - A Force Diagram describes how a product should be tested. Intertek engineers base the creation of Force Diagrams on our knowledge of foreseeable use, critical manufacturing process and critical components that have high potential to fail.
- Test-to-Failure (TTF) - Unlike any legal testing, TTF tells manufacturers on how many defects they are likely to find in every million units of output. This information is incorporated into the process and concludes if a product needs improvement in quality or if it is being over engineered, which will eventually lead to cost savings.
- Intervention - Products are separated into groups according to the total production quantity and production lines. Each group then undergoes an intervention. The end result is measured by Z-value, which is the indicator of quality and consistency of a product to a specification. Intervention allows manufacturers to pinpoint a defect to a specific lot and production line; thus saving time and money in corrective actions.
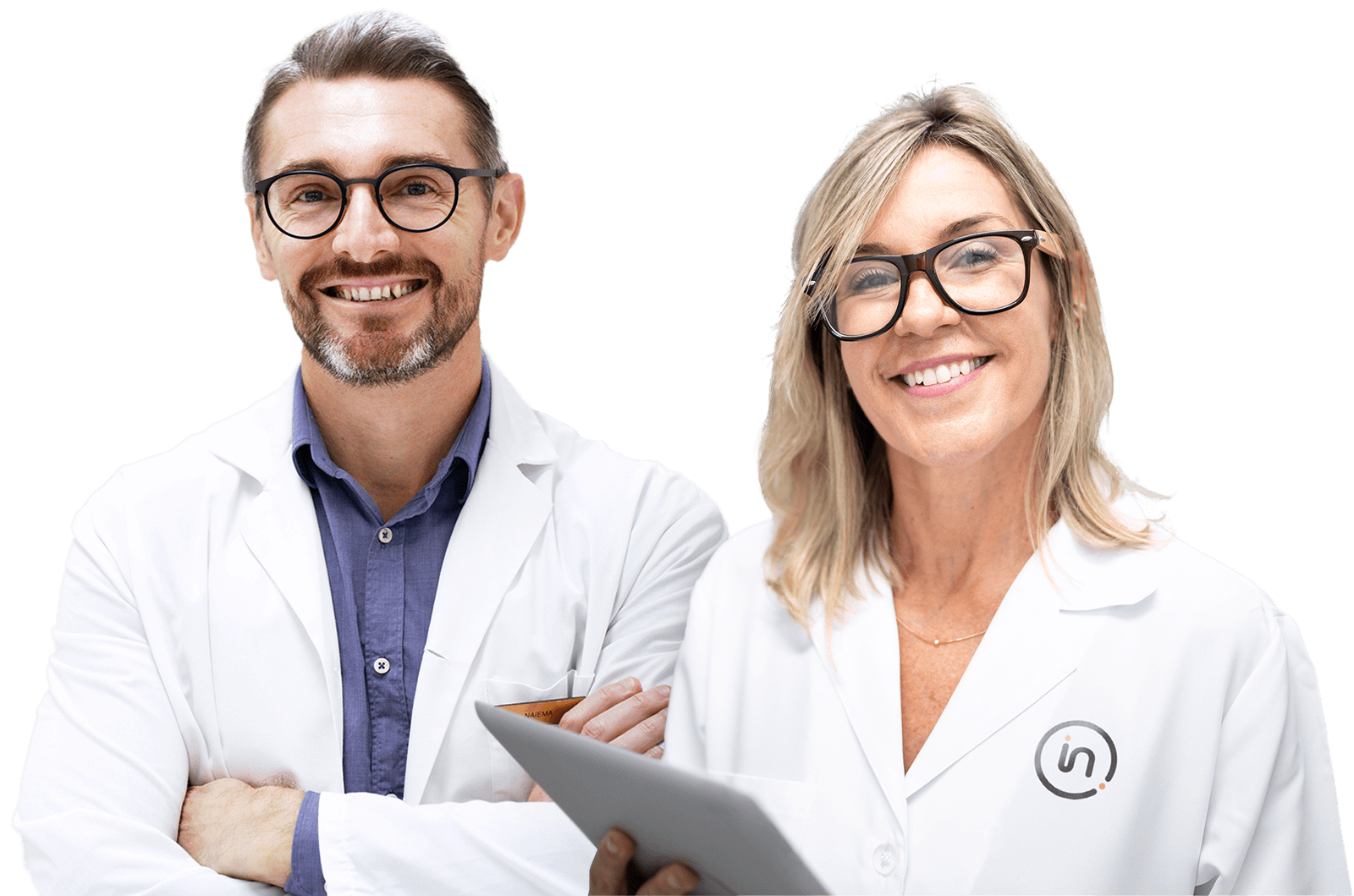